52.36 Kw Copper Wire Granulator Separator 300-400 Kg/H 4300×1950×2400 Mm
Product Details:
Place of Origin: | Henan, China (Mainland) |
Brand Name: | TMS |
Certification: | CO, ISO |
Model Number: | TMS-600 |
Payment & Shipping Terms:
Minimum Order Quantity: | 1 set |
---|---|
Price: | negotiable |
Packaging Details: | One 20 feet container |
Delivery Time: | 15 work days |
Payment Terms: | L/C, T/T, Western Union |
Supply Ability: | 30 sets per month |
Detail Information |
|||
Application: | Scrap Copper Cables | Type: | Dry Type |
---|---|---|---|
Power: | 52.36kw | Function: | Crush And Separate Copper From Plastic |
Separating Rate: | 99.9% | Output: | 300-400 Kg/h |
Weight: | 3400kg | Warranty: | 12 Month |
Highlight: | copper wire granulator separator,copper cable granulator machine |
Product Description
Model 600 capacity 300-400 kg/hcopper wire granulator and separator for sale
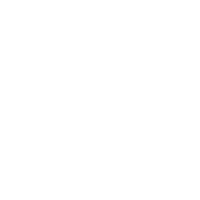
Copper wire granulator and separator is used for recycling scrap copper wires/cables with diameter less than 25mm, better for single conductor diameter of 0.2-0.5mm. The wire is like auto wires, communication cables and kinds of miscellaneous wires and cables.
copper wires are shredded by crushers, then plastic and copper granules are separated by vibration and airflow. They come out from different outlets, dust is collected by dust collector. The copper granules and plastic granules will be separated by small vibrator twice time. The recovery rate can reach 99.9%.
Size (mm) | Capacity | Wire diameter range | Power | Voltage | Weight |
4300*1950*2400 | 300-400 kg/h | 0.1-20 mm | 52.36 kw | 380/240V | 3400kg |
The spare parts of copper wire granulator and separator includes screen mesh and blades in crusher.
Start or Stop the Machine
1). Start the Machine
Start the machine by first pressing the Run button on the bottom black panel, then pressing the left Start/Stop button to adjust the bottom air; generally, when the number is around 52, press the Run button again and number is settled. Then press the buttons from Right to Left for starting the machine.
There is an interval of one minute between pushing two buttons. Feed wires into the machine after the machine is completely started. Observe the output and adjust the bottom wind accordingly.
2). Stop the Machine
Push buttons from Left to Right for stopping the machine
There is an interval of one minute between pushing two buttons
3). Emergency Stop
In emergency cases, the Emergency Stop button (the big Red Color) must be pressed to stop the machine. If you want to start the machine again, first reset the Emergency Stop button by turning it clock wisely.
Installation & Operation Safety
1). Machine installation should be smooth and safe grounding must be ensured. Enough room must be kept for operation.
2). Power must be supplied in comply with requirements of the machine, and make sure the turning direction is the same with the markings on the machine. (Turning in wrong direction will cause the blade roller damaged and the manufacturer will not take any responsibility for the problems caused by this.)
3). Check whether the bolts at each part get loose, turn the blade roller of the Chopper by hand and make sure the space between fixed blades and rotating blades is 0.15mm-0.25mm. The machine can only be started when there is no collision between blades.
4). The machine must be started without load.
5). Hands must not be put into the machine in material feeding process.
6). Safety precautions must be taken when blades are being dismantled and replaced to prevent the blade roller from rotating.
7). Operators must wear protective gloves when dismantling or changing blades.
8). Non-designer personnel shall not change the wiring, program or other diameter settings in the Power Control Panel, or it may cause mal-functions.
9). Regular maintenance of this machine is necessary and lubricant should be injected and replaced regularly, this will reduce wear and tear in working and lengthen the service life.
10). Regular inspection for blades and blade roller is necessary. When blades are found loose they must be tighten immediately; if cracks are found in blades, the blades must be replaced immediately.
After-sale service
1. The machines except spare parts are guaranteed for 12 months.
2. Engineer will be sent to your place to guide how to operate for the production line.
3. We will send you extra set of spare parts and two sets small vibrators.