99% Purity Dry Type 100-150kg/H Copper Wire Granulator
Product Details:
Place of Origin: | Zhengzhou, China |
Brand Name: | TMS |
Certification: | CO, ISO, CE |
Model Number: | Mini-400 |
Payment & Shipping Terms:
Minimum Order Quantity: | 1 Set/Sets |
---|---|
Price: | US $10,000-13,000 / Sets |
Packaging Details: | Scrap copper cable crusher and separator machine is packed with standard export ply wooden case. . |
Supply Ability: | 30 Set/Sets per Month Scrap copper cable crusher and separator machine |
Detail Information |
|||
Name: | Copper Wire Granulator | Type: | Dry |
---|---|---|---|
Power Supply: | 11.92kw | Function: | Recycle Copper |
Copper Purity: | 99% | Capacity: | 100-150kg/h |
Color: | Red | Net Weight: | 750kg |
High Light: | 150kg/H Copper Wire Granulator,99% Copper Wire Granulator,99% mini copper wire granulator |
Product Description
99% Purity Dry Type 100-150kg/H Copper Wire Granulator
Description of copper wire granulator
With the improvement of environmental protection awareness, more and more people begin to enter the research of industrial waste reuse. Waste recycling has become a hot project in recent years. It is a resource recovery engineering technology developed with the production chain of environmental protection and energy in recent years. It has become one of the important deep-processing technologies of industrial minerals and other raw materials. It is of great significance to the industrial development of modern high-tech waste resource recycling production technology.
The screening process used by the traditional copper wire granulator requires water. When the crushed raw materials are put into the water, the plastic will float up automatically and the metal will sink automatically. The buoyancy is used to screen out the plastic and metal. The principle adopted by the dry copper wire granulator is separation, that is, specific gravity separation, The production process of copper wire granulator production line is: Waste wires and cables - primary crushing - vibration separator - dust removal - secondary crushing - bucket elevator - high voltage electrostatic separation equipment - separation is completed.
Technical parameter of copper wire granulator
Model | Size | Capacity | Wire diameter range | Power | Volage | Wight |
Mini-400 | 1500*1500*1900 mm | 80-100 kg/h | 0.1-20 mm | 11.92 kw | 380/240V | 750kg |
TMS-400 | 2700*1900*2300 mm | 150-200 kg/h | 0.1-20 mm | 23.12 kw | 380/240V | 1200kg |
TMS-600 | 4300*1950*2400 mm | 300-400 kg/h | 0.1-20 mm | 52.36 kw | 380/240V | 3400kg |
TMS-800 | 9200*4100*3540 mm | 500-600 kg/h | 0.1-30 mm | 71.86 kw | 380/240V | 4100kg |
Features of copper wire granulator
1. Integral combined structure, small floor area, convenient for movement and transportation;
2. The operation is simple, and only one operator is needed in the whole process;
3. The sorting system adopts multi-layer multiple high-precision sorting and frequency conversion control, and the sorting rate can be as high as 97% - 99%;
4. The crushing system adopts high-strength alternating cutter shaft with high efficiency, and the cutter is made of special alloy.
5. The operation process of the equipment is closed, with bag dust removal and air filtration system to ensure material loss and dust emission.
Separation effect of copper wire granulator
1. During the first trial production, the feeding amount should be controlled at about 50% - 60% of the machine's output. After continuous production for 3-5 hours, the output should be increased one after another. The output should be increased by 10% every 3-5 hours. It is not allowed to load at the beginning, because each machine needs running in process.
2. The dry-type copper wire granulator is filled with new grease every 40 hours, and the crusher bearing is filled with new grease every 8 hours. The lubricating grease is 3# calcium grease.
3. During production, raw materials should be classified and broken, and copper wire and aluminum wire should not be mixed together. The diameter of each batch of broken raw material line should be the same, and the mixing of thick line and fine line will affect the separation effect.
4. During commissioning, the feeding amount should be controlled at about 30% of the machine output, so as to avoid the accumulation of tail machine materials caused by untimely single machine adjustment.
5. The speed frequency of downdraft fan frequency converter is adjusted to 35-40hz for the first time, and the value is increased or decreased according to the sorting condition. For the first time, the speed and frequency of the vibration sorting motor frequency converter are adjusted to 28-35hz, which is increased or decreased according to the sorting situation.
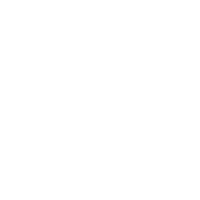